- Accueil >
- Security and Safety Insights >
- Case Study: Cushman & Wakefield's Best-in-Class Lockout-Tagout Program
Case Study: Cushman & Wakefield's Best-in-Class Lockout-Tagout Program
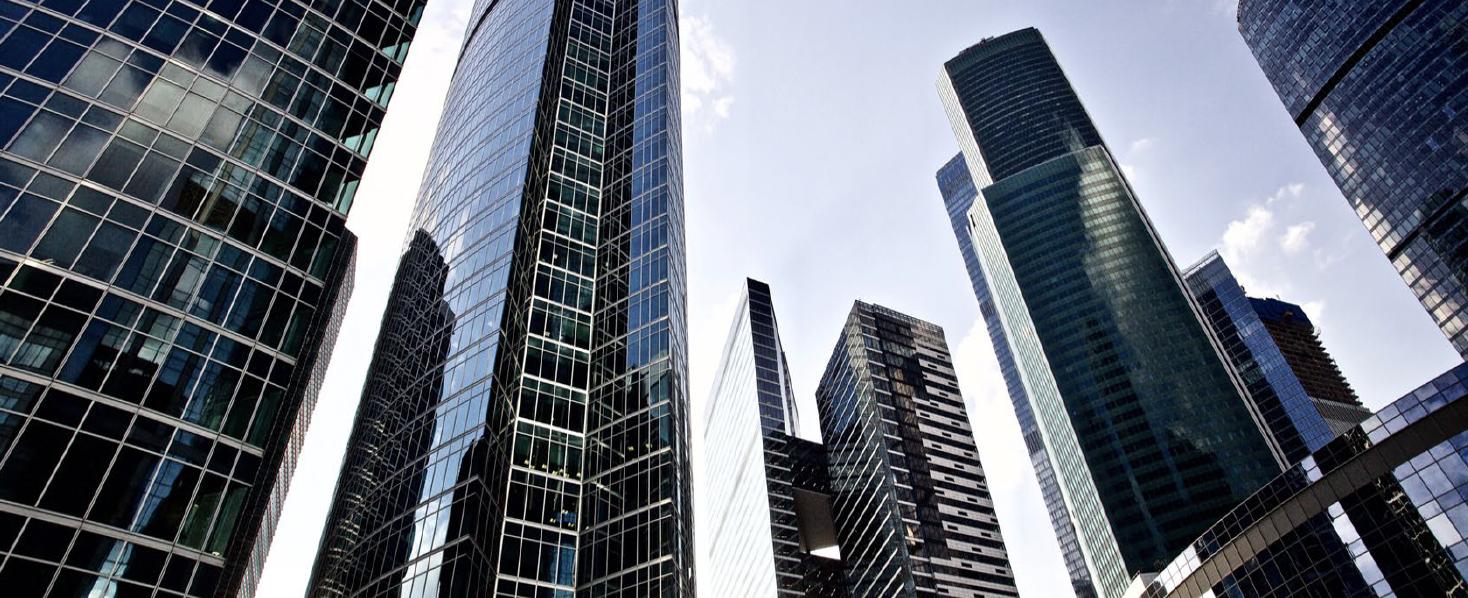
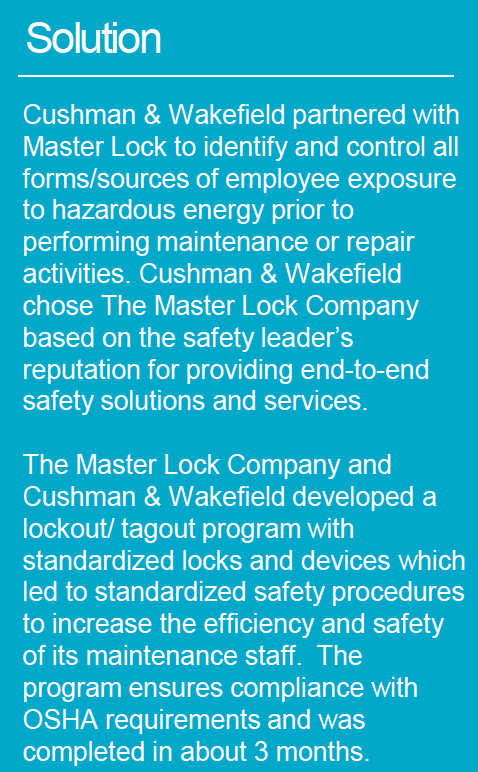
Cushman & Wakefield (C&W) is a global leader in the commercial real estate industry that operates in 60 countries and employs more than 50,000 people. C&W maintains buildings for its clients and currently manages over 4.3 billion square feet of commercial space. Understanding that maintaining these facilities creates risks for employees, C&W committed to a partnership with Master Lock to enhance their Lockout/ Tagout (LOTO) safety standards.
Goal & Outcomes
Developing a Best-in-Class Lockout-Tagout Program
C&W made the decision to implement a best-in-class approach to a critical aspect of safety for a large financial institution client that has many small and large facilities located throughout the US. The initial phase included an evaluation that was instrumental in understanding quantities and types of equipment that would require a written lockout procedure throughout their client’s facilities. In addition, the evaluation offered the opportunity to designate type and quantities of lockout equipment needed to perform the lockout procedures as part of the larger second phase of the project. The written procedures provide Authorized Employees a step-by-step approach to isolating hazardous energy and achieving a zero-energy state on the equipment they are servicing and maintaining.
The outcome of the second phase entailed the development of over 5,100 written lockout procedures across the 25 client locations. The procedures provided to the client are visual placards that identify the hazardous energy related to a piece of equipment and the energy isolation points indicated by serialized identification tags and corresponding to each step of the energy isolation procedure. Each procedure is hung at the point of use, available for the next maintenance task. With its partnership with Master Lock, C&W was able to train a standardized equipment and a lockout procedure methodology for the control of hazardous energy to all Authorized and Affected personnel though this best practice approach.
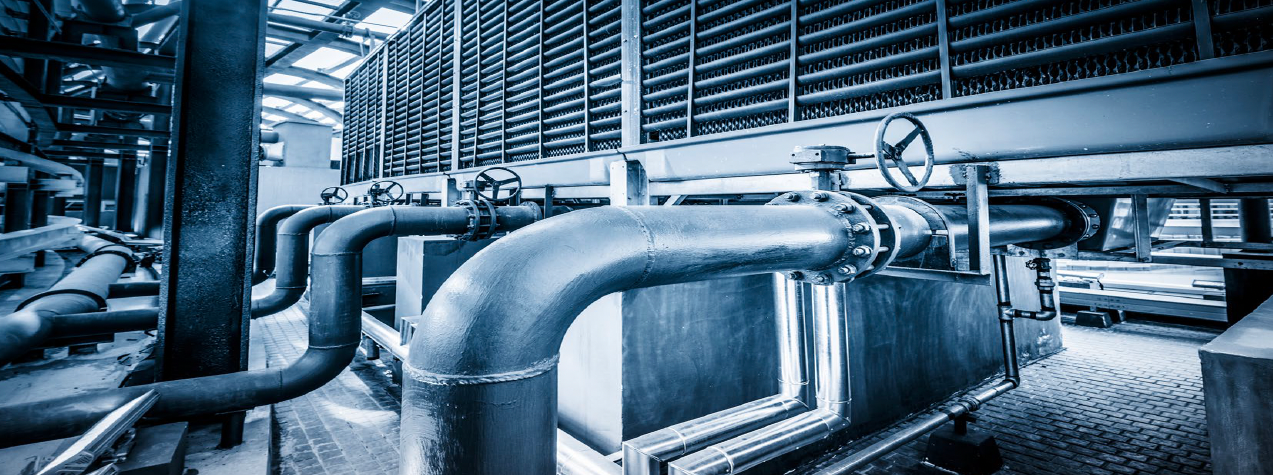
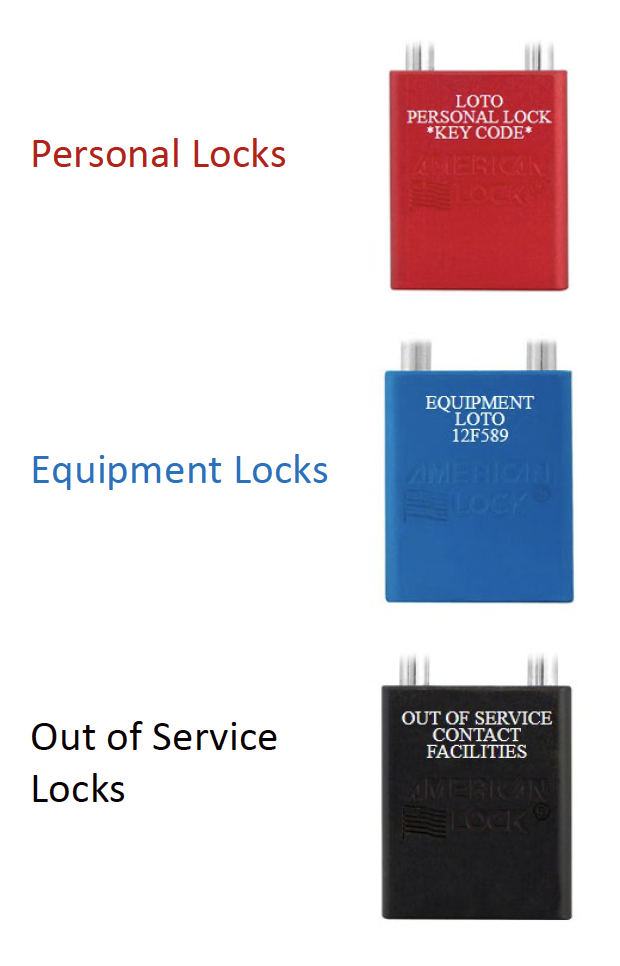
The following are solutions and standards put in place to address Cushman & Wakefield’s safety challenges:
Lockout/Tagout Standards Established
At the start of this initiative, C&W partnered with Master Lock to establish standards for the safety padlocks used: personal locks, equipment locks, and out of service locks.
• Personal Locks are for one authorized individual to control an energy isolation point and ensure it remains in the zero energy or off position. Authorized persons always control the keys to their personal locks and the locks must identify their owner by a tag or label. Personal locks are keyed alike in sets with one key per set. The key number is engraved on all the locks in their respective set.
• Equipment Locks are used on equipment in group lockout or multi-isolation point situations where there are insufficient personal locks. The keys to the equipment locks go in a lock box and then authorized persons place their personal locks on the lock box. These locks are keyed different, and laser engraved with the key code of their key.
• Out of service Locks (or Departmental locks) are used on equipment that have been rendered inoperable for an extended period. Out of service locks shall not be used for a controlled LOTO under any circumstances. A departmental lock is used to administratively prevent the unauthorized use of equipment. A group, like facilities maintenance, rather than an individual may control a departmental lock. These locks are all keyed to the same key.
Continual Updates to Procedures
To ensure that the procedures are continually maintained, an annual audit will be conducted to align with maintenance work. Any changes or updates identified will be integrated into the procedures and communicated to maintenance personnel.
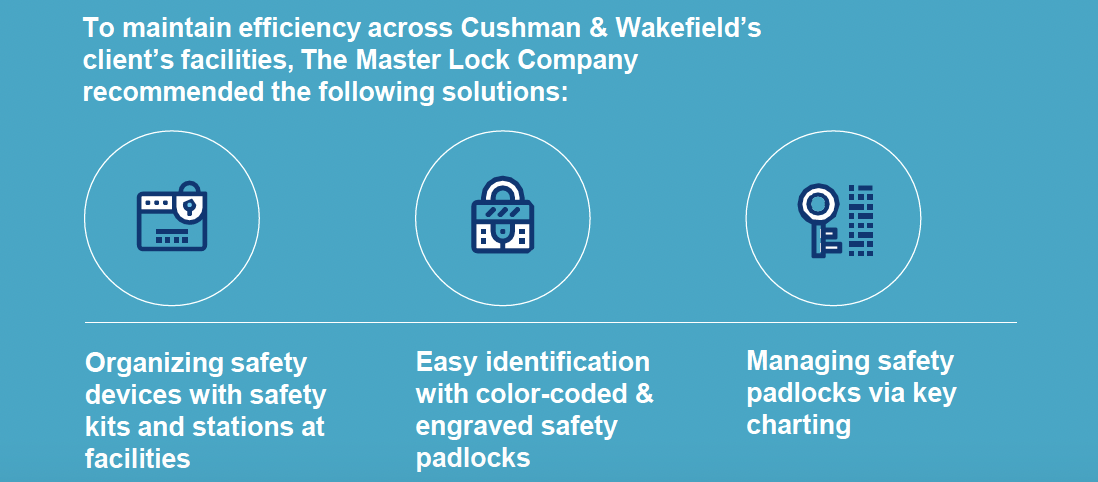
Organizing safety devices with safety kits and stations
In addition to safety padlocks, C&W needed to provide its maintenance staff with the safety devices necessary to perform the lockout of the energy sources. These devices include gate valve lockouts, circuit breaker lockouts, adjustable cables, and more. To ensure that employees had the devices needed, safety kits and/or wall-mounted safety stations were purchased that contain the devices needed to perform lockout at a given facility.
Easy identification with color-coded and engraved safety padlocks
C&W and Master Lock partnered to set up its LOTO safety standard by designating padlocks for specific maintenance activities. C&W implemented Master Lock’s American Lock branded color-coded safety padlocks. They utilize three different padlock colors so that all maintenance employees can visually recognize the type of lockout being performed. Personal locks are red, equipment locks are blue and out of service locks are black. The locks are engraved with the key code of the key.
Key charted safety padlocks
With over 200 maintenance employees across 25 facilities, C&W is utilizing Master Lock’s key charting system to manage key codes within facilities, and in the case of personal locks, across employees. The Master Lock Company’s key charting system helps to mitigate any unwanted key duplication within each facility and across all employees. This service is available at no extra cost.
EHS framework at Cushman & Wakefield
C&W integrates, aligns, and executes EHS as an integral part of their operational framework. Given that hazardous energy is a high-risk employee exposure, the decision was made to focus on creating a best-in-class program that centered around providing a simplified and consistent approach to LOTO at each of the client sites. The result was moving beyond compliance and creating a LOTO standard that provides a high level of safety and reduces risk.
In addition, this investment provided significant value to C&W’s client through risk mitigation and developing LOTO procedures specific to the assets owned and/or managed by the client
Employee training
In order to implement the new LOTO standards, C&W conducted training for all employees who are authorized to perform LOTO at any of the 25 client facilities (over 200 employees). The training ensures that each employee in conducting relevant maintenance tasks not only was trained on the procedures but were able to demonstrate competency in performing LOTO properly.
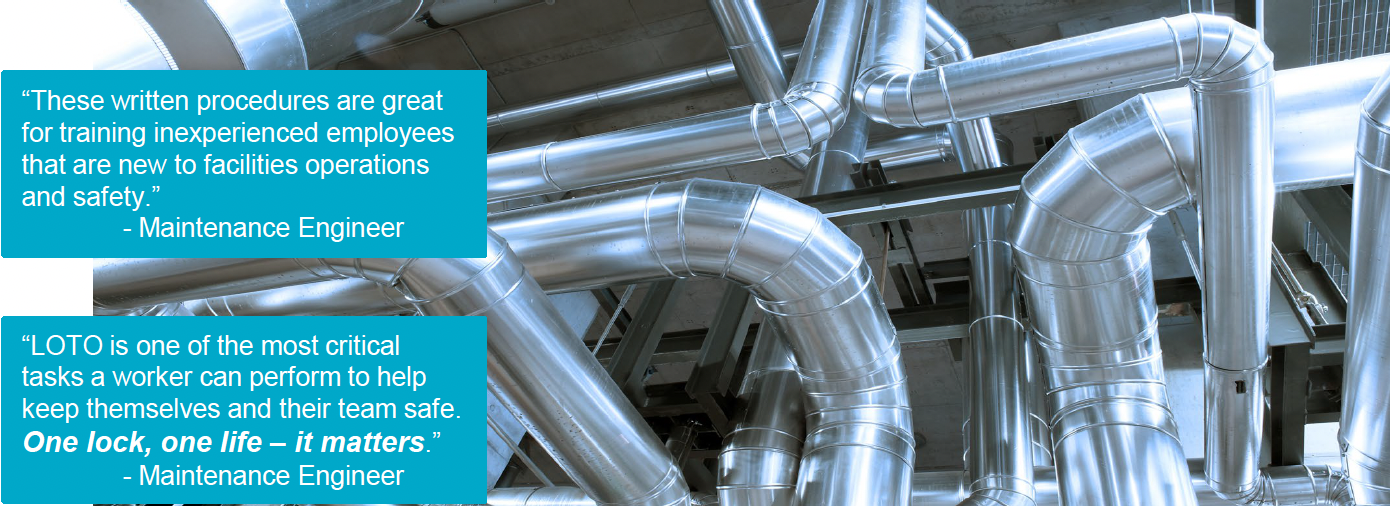
Results
After implementing LOTO energy control procedures at 25 client facilities, C&W has created a consistent lockout/tagout safety program with standardized safety locks, devices, and procedures that ultimately created a safer work environment for its employees.
Specific results include:
- A risk assessment was conducted and found a 45% reduction of risk in LOTO after implementing theprogram.
- Results from a recent survey of maintenance employees found: 95% of employees feel the new onsite LOTO procedures are more helpful in eliminating the flow of energy on assets versus what they were doing previously, and nearly all maintenance staff find the new LOTO procedures easy to follow.
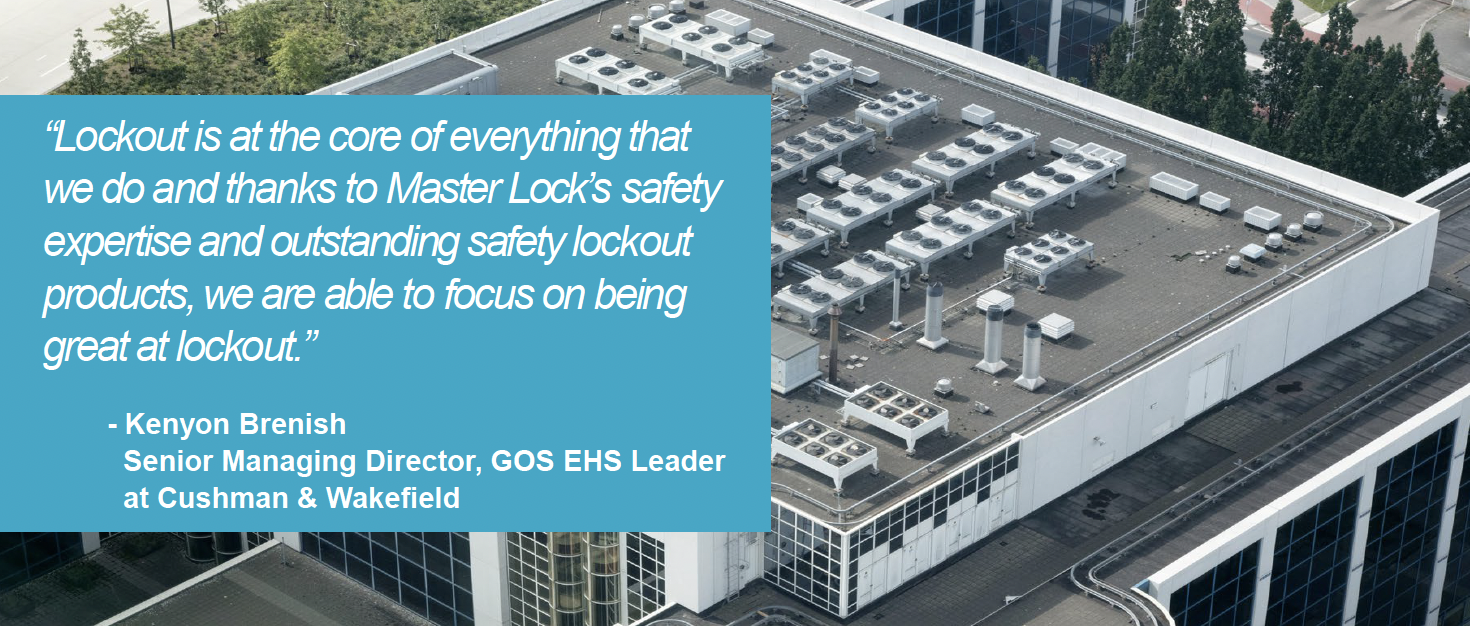
TESTIMONIAL
“The level of customer service was second to none; anytime I reached out with a question or asked Master Lock to look things over, the answer was always ‘yes’. Most importantly we drove a consistent standard and provided a much higher level of safety with our program, moving beyond compliance, and creating a best-in-class LOTO program.Master Lock has proven to be a great safety partner and I’d recommend their safety products and services to any company looking to implement a superior LOTO program.”
–Brandon Neill, Senior Manager –Environmental, Health, Safety at Cushman & Wakefield
Have a similar challenge? Don’t know where to start? Contact one of the Master Lock safety experts to start a conversation to see how we could help.
Visitez MasterLock.com to learn more about Master Lock’s Professional Lockout Services.