- Accueil >
- Security and Safety Insights >
- Making Your Lockout and Tagout Procedures Efficient
Making Your Lockout and Tagout Procedures Efficient
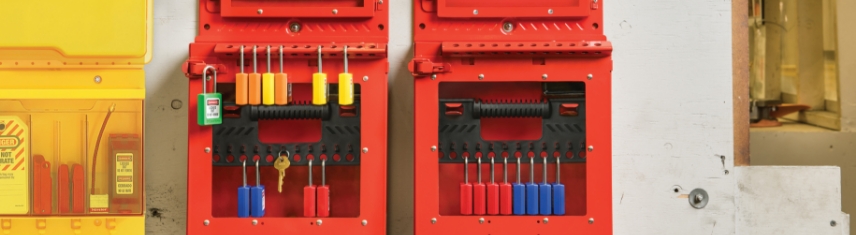
Anyone responsible for the safety of maintenance and operations teams has a lot on their plate. Not only do they have to ensure compliance and safety, they’re also held accountable for operational efficiency. However, with the right approach to lockout and tagout procedures, it’s possible to keep workers safe across facilities, without sacrificing efficiency.
Understanding OSHA Regulation 29 CFR 1910.147
In 1989, OSHA developed a new standard for the control of hazardous energy, 29 CFR 1910.147. It addresses the need to take machinery and equipment to a state of zero hazardous energy before commencing maintenance or service activities – and for good reason. Without proper hazardous energy isolation, operations and maintenance personnel face the risk of serious or fatal injury while performing such duties. Hazardous energy control programs and lockout procedures can help ensure a safe work environment for employees – and peace of mind for safety supervisors.
In compliance with OSHA 1910.147 comes the need for accountability and efficiency to ensure procedures are followed correctly and in a manner that maximizes uptime. Choosing the right lockout equipment can help effectively support lockout goals and drive accountability and efficiency. Having a clear understanding of who is asked to lockout equipment and the type of lockout activities they are engaged in is essential in choosing the most effective lockout solution for your organization.
OSHA’s Requirements & Criteria for Lockout Equipment
OSHA standard 29 CFR 1910.147 identifies five criteria for lockout equipment, including safety padlocks - addressing both the physical environment and the visual.
Physical environment
The structural design and materials of construction should be conducive to your operating environment. Special consideration should be given for harsh operating environments characterized by the presence of corrosives or particulates that the locks are exposed to and may affect functionality over time. For the harshest environments, build a plan for periodic maintenance and replacement to ensure your team is equipped with the best equipment. In other words, safety padlocks must be durable and substantial.
Durable - Capable of withstanding the environment to which they are exposed, including weather, temperature, chemicals, etc.
Substantial - Reduce the likelihood of early or accidental removal. The lock remains secure and in place under the stresses and forces one should reasonably expect during lockout.
Visual
Visual cues are integral to lockout as they offer clues as to whether policies and procedures are being followed by the designated authorized employees for a specific maintenance task. This is an important consideration when choosing padlocks as they can help you build accountability and efficiency into your system. OSHA states that the padlocks should be standardized, identifiable, and exclusive for safety. They should also be tailored specifically to your facilities needs.
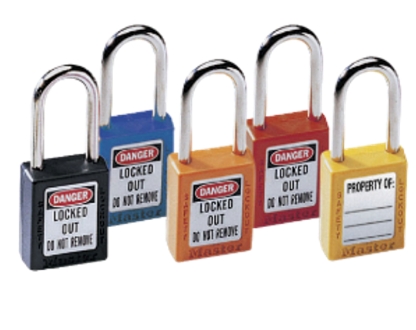
Standardized - The use of colors, shapes, sizes of padlocks and labels help to differentiate within a lockout padlock system and from other padlocks in or around the facility. Some may choose to segment their maintenance operations by craft, or department or even facility. Others may segment by the application of the lock, whether it is for personal locks, job locks, transfer locks, or control locks. In many cases it’s a blend of both approaches.
To meet the requirement for standardization, lock specifications should be assigned to each segment. These specifications can and should include the color of the lock and factory engraved markings on the lock. This process of standardization helps drive accountability. Supervisors should be able to read a lockout procedure or safe work permit, understand the nature of the work being done, and tie out the locks to the task and workers.
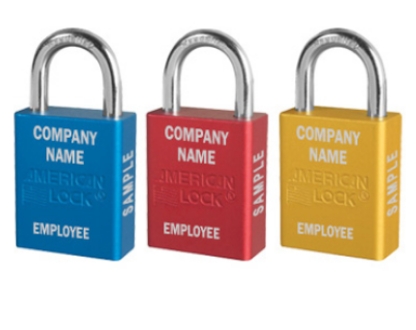
Identifiable - Types, colors and labeling of padlocks also help to support identification. For example, if a servicing task requires the support of an electrician and blue was assigned to electricians, they would look for blue locks at the energy isolation points or on one of the group lock boxes assigned to the job.
Marking on locks can provide an indication to ownership – whether it be an employee or department – and it can help identify a set of locks. This helps those inspecting a lockout understand each person performing work is protected by their own padlock. When multiple people are working, it helps them identify their padlock for removal when the work is done. And, if an employee completes the work but forgets to remove their padlock, supervisors will know who to contact.
In facilities where group lockout is prevalent, keyed alike padlocks in various set sizes are established and at the ready for the next job. It is common to engrave or label the key number, set size and a sequential number on each lock within a set. Doing so helps lockout coordinators quickly identify when a lock is missing and facilitates the process for ordering a replacement.
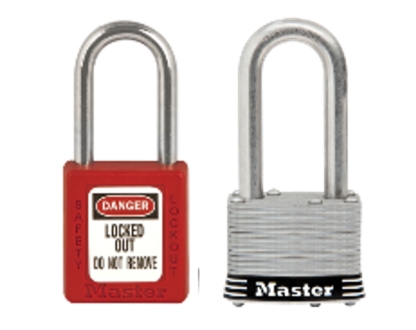
Exclusive for safety - It’s critical that authorized and affected employees recognize lockout without any ambiguity. Visual cues, such as color by department or type of lock, are an extremely important aspect of a lock management system. Designate specific colored locks and make them exclusive to lockout so they are not easily confused with other applications, such as security.
The presence of the lockout padlock signals to both authorized and affected personnel that lockout is taking place. It signifies an employee is performing maintenance activities and that equipment has been taken to a state of zero energy in order to do so. It also indicates a safe work environment is secured by the padlock and those in the area should not mess or tamper with the lock.
How Compliant Safety Padlock Systems Increase Operational Efficiency in Lockout and Tagout Programs
After understanding what OSHA considers “compliant” lockout equipment, safety managers should then consider how lockout options contribute to efficiency.
Leveraging visual cues
Upon seeing a safety padlock, one should be able to discern what lockout process is taking place and/or who is participating in the lockout. Select padlock features and options (color) that visually communicate this information to supervisors. They could be organized by:
- Maintenance, electrical, HVAC, etc.
- Personal, equipment, contractor, control, transfer, etc.
Installing and removing padlocks
With the understanding of how many locks are commonly applied during various lockout processes, lock features can be selected to make the application and removal of the locks efficient and frustration-free.
One consideration is how many locks are going to be applied on a typical job. If the answer is “multiple,” it’s important to consider the type of key system and key management that make padlock installation removal simple. Two commonly implemented key configurations are “keyed-different” and “keyed-alike”:
- A lock that has its own unique key is keyed-different. If an employee is most commonly applying a single lock, a keyed-different lock is recommended. If four locks are commonly applied for each job, keyed-different locks are sufficient, but there's a one in four chance the first key pulled out of an employee's pocket will open the lock.
- A set of keyed-alike locks will all open with a shared key. The more locks that are applied, the more important it is to use a keyed-alike system. Keyed-alike is common for job locks used in the execution of group lockout. Job locks can be structured in keyed-alike sets of just a few locks can be structured in keyed- alike sets of just a few locks all the way up to hundreds of locks commonly utilized for major turnaround projects in petrochemical and power generation facilities.
No matter what keying method is chosen, managing keys within a facility is critically important. The integrity and security of lockout can be compromised when other keys in the facility can open another authorized employee’s padlock. Master keys and duplicate keys in the facility need to be carefully managed and the policies and procedures for accessing these keys should be explicitly outlined within a site-specific lockout policy
Additional padlock feature
- Adding information to the locks and keys can help identify which key opens which lock, can single out locks missing from a set, and can identify who owns the lock.
Deployment of lockout equipment within facility
A final opportunity to optimize efficiency is to understand how personal locks are deployed to support routine machine servicing and changeovers. Unproductive movement impacts efficiency, which is especially important for quick turn maintenance activities. Target 15 seconds as the maximum time it should take to access padlocks and other lockout equipment. Consider these ways to simplify rapid access to lockout equipment:
On person
If an employee must cover a lot of physical area and the number of locks typically required for lockout is nominal (2-3), it makes sense to assign locks to the individual.
At point of lockout
If there is equipment that must be locked out frequently (i.e. as in the case of frequent changeovers) or a piece of equipment requires a relatively high number of padlocks and lockout devices, consider placing the equipment at or near the machine, available for the next maintenance or changeover event.
Equipment audits
To ensure you are prepared for the next job, information on the padlocks helps identify padlocks that need to be found or padlocks that need to be replaced. A durable and clearly identifiable marking is ideal.
Master Lock provides professional services that can help organizations through the whole process – from facility assessments, to development of written procedures, to charting safety padlocks to prevent duplication of keys, and more.